Contact
86-539-3101518
Fax: 86-539-3101518
Mobile: +86-15969943322
+86-18853986768
Official website: www.xrdplymachine.com
MIC website: http://xrdplymachine.en.made-in-china.com
Email: Jasonqiao@xrdplymachine.com
Factory address: No.1 Zhubao wood industry zone, Lanshan district, Linyi-276000, Shandong,China.
Office: F16, Amethyst mansion, Linyi, Shandong,China.
LOCATION:HOME > PRODUCTS > OSB/Particleboard Machine > OSB/Particleboard Machine
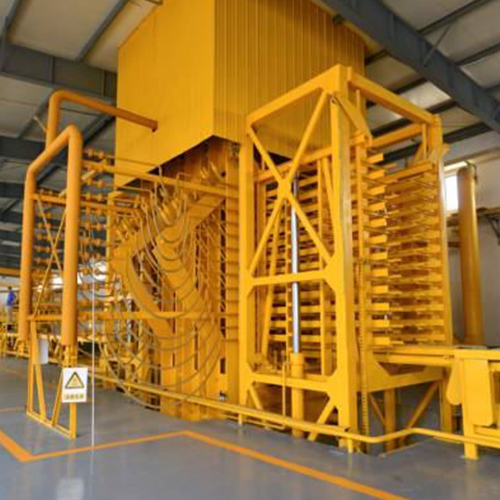
Particleboard Production Line
Date: 2021-12-22 08:57
View:
About us:
CHINA XINRUNDE COMPANY is a technology company serving the wood-based panel industry worldwide. Founded in 1989 year and located in worlds biggest wood-based panel production base -- LINYI City, which is famous for manufacturing all kinds of veneer, plywood, blockboard, particle board, LVL, MDF,HDF etc.. Thanks
Date: 2021-12-22 08:57
View:
About us:
CHINA XINRUNDE COMPANY is a technology company serving the wood-based panel industry worldwide. Founded in 1989 year and located in worlds biggest wood-based panel production base -- LINYI City, which is famous for manufacturing all kinds of veneer, plywood, blockboard, particle board, LVL, MDF,HDF etc.. Thanks
Detailed introduction
Brief instruction of OSB/PB
Brief description of production process
1 · Shaving preparation section
Wood raw materials are transported to the factory and stacked according to tree species.
Option One:
Wood, sticks and other short materials, feeding belt conveyor for drum chipper. The qualified wood chips cut by the chipper are sent to the wood chip silo for intermediate storage via the discharge belt conveyor and bucket elevator. The wood chips are made into qualified wood shavings by a ring shaving machine and sent to the wet wood shaving bin by wind.
Option II:
The wood raw materials are fed into the long wood chipper by the loading conveyor, and then cut into qualified shavings at one time. The wind is sent to the wet shaving bin.
third solution:
Long wood such as small diameter wood is fed into the long wood chipper by the loading conveyor and cut into qualified wood shavings at one time. The shavings wind is sent to the wet planing silo. Zhiya and other short materials, feeding belt conveyor for drum chipper. The qualified wood chips cut by the chipper are sent to the wood chip silo through the wood chip wind for intermediate storage. The wood chips are made into qualified wood shavings by a ring shaving machine and sent to the wet wood shaving bin by wind.
2 · Drying and Screening Section
The shavings output from the wet bin are sent to the rotor dryer via screw conveyor. The dried shavings are then sent to a screening machine by a screw conveyor for screening. The discharge screw conveyor of the dryer is equipped with a spark detection device. Once the alarm is issued, the dry material can be automatically discharged out of the system. The coarse shavings that have been screened enter the re-crusher for further processing, and together with the medium coarse shavings that have been screened, they are sent to the air flow sorter by a screw conveyor for sorting. The qualified fine materials that have been screened out are sent to the surface shaving silo. The qualified materials sorted by the air-flow sorting machine are sent to the core shavings bin for intermediate storage. The sorted coarse material enters the grinder and is crushed, then combined with the fine shavings screened out and sent to the surface shaving bin. According to the different proportions of the surface and core layer shavings when producing different plate thicknesses, the coarse shavings in the part can be quantitatively transferred to the sander to make surface shavings.
3 · Adhesive supply section
Including preparation and delivery of paraffin emulsion and curing agent solution, storage of additives and preparation and application system of mixed glue. The table and core layer mixed glue is configured in a centralized glue mixing machine. The preparation and application system of the mixed glue is set by PLC program control. Automatic metering, continuous configuration, quantitative application, and adjustment can be implemented according to the process regulations.
4 · Sizing Section
Surface and core shavings are glued separately. The wood shavings are output quantitatively from the silo, pass through the vibrating feeder, and are continuously weighed by the metering device, and then enter the ring rubber mixer in a balanced manner. The glue mixer makes the entered wood shavings and the atomized glue liquid fully mixed, uniformly glues, and automatically adjusts the glue application amount according to the change of the wood shavings conveyance to keep the rubber ratio set by the process constant.
5 · Hot press section
After the glue is applied, the surface and core shavings are sent by the belt conveyor to the mobile air-laying machine. Two sets of opposite air-jet nozzles blow the shavings out. On the mesh belt of the forming conveyor, the upper and lower surfaces are fine and uniform, with a gradient structure Particleboard slabs. The formed particle board slab is cut to the required length by a cross saw, and the scrap is returned to the paving machine through the air delivery system. After the single-layer hot press is hot-pressed, the forming conveyor simultaneously transports the raw board out of the press and the slab into the press. At the same time, the paving machine moves quickly in the same direction. When it is in place, a new slab is laid. Unqualified slabs can be returned to the wet silo for recycling through the recycling device.
6 · Saw Edge Section
The pressed wool board enters an out-of-board stick conveyor with a scale, is centered and weighed. The centered and weighed wool board enters the longitudinal and horizontal sawing machine, and the wool board is saw into a flush board. Chipped scrap can also be returned to the wet bin. The edge plate is stacked by the roller conveyor through the stacking centerer and the hydraulic lifting platform, and then sent to the forklift roller platform, and then sent to the intermediate storage by the forklift.
7 · Sanding Section
The stored boards are sent to the sanding system. The sanding system consists of a hydraulic lifting platform, a roller conveyor, a broadband sander, and the like. After sanding, the finished boards are sent to the finished product warehouse after inspection and classification.
8 · Electric control system
The particleboard production line has a main control room, from particleboard measurement, sizing, forming, hot pressing to full-edge weighing, and it can be operated automatically or manually according to the programmed PLC program. In addition, operating stations (boxes) are set up at the operation site of each section (except the molding and hot pressing section) to control and monitor the operation of the equipment in this section.
Please fill in your procurement needs and contact information